Andy Trainer
24 May 2011
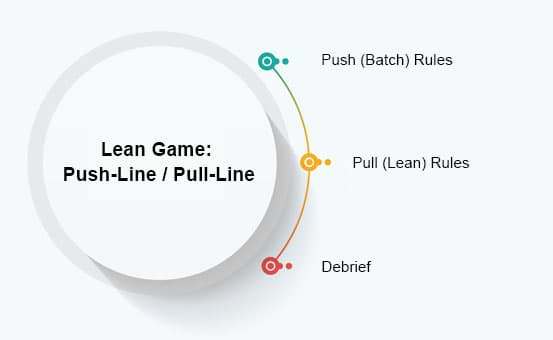
Lean Game: Push-Line / Pull-Line
As part of our Lean Training and Six Sigma Training courses we often use
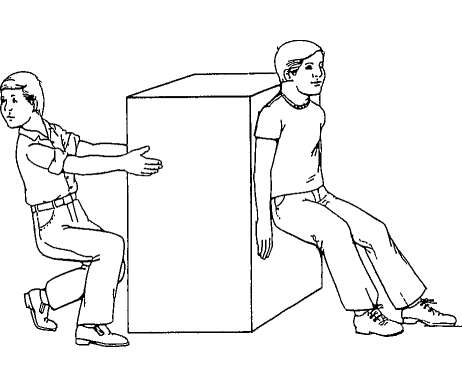
training aid, if you're trying to make a business case for
Lean Games to illustrate key points.As well as being a great Six Sigma
Here we describe the Push-Line / Pull-Line Lean game...
Lean Game: Push-Line / Pull-Line
This Lean Game takes around 25-30 minutes to complete. It's purpose is to highlight the advantages of the Lean approach to assembly lines (pull) over the batch approach (push).
How to Set Up:
- You'll need around 50 sheets of white paper and a few of a different colour - say green.
- Get four of your colleagues in a line with their own work area on a desk in front of them. Leave enough space between work areas for pieces of paper to be passed. When you start, person A’s output area will become B’s input area, and so on.
- Find a simple paper folding or origami project (e.g building a paper hat) and show each person a stage in the production process. Give the first person an easy job (e.g. just the first fold) the second folder a slightly more difficult job (e.g two folds), the third person harder still (all the remaining folds!) and give the last person a very easy job again. (e.g. throw the hat in the bin).
- Explain to the workers that they will be using two different sets of rules.
- Start the process with push (batch) rules and run the process for a while before switching to the pull (lean) rules.
- Debrief with everyone at the end to discuss the results.
Push (Batch) Rules
Each person follows these work rules in the Batch method:
- When the work area in front of you is empty, get an item from the input area designated to you to work on.
- When you complete your part of the process, place the item in your output area.
Using these rules, it won't be long before the person working on the third station has a lot of work piled up in front of them! When this happens, ask the first person in the chain to begin work on a green piece of paper and stop the process.
Pull (Lean) Rules
Using the pull (Lean) system - use the following work rules.
- If work area AND output area are empty, take an item from your input area and complete your stage in the process.
- When you finish your part of the process, put the item in your output area.
Once 3-4 items have come through the system, put a green piece of paper in and stop.
Debrief
If the game above has worked to plan, it should bring out the following comparisons to go through with the process team:
- The push system generated piles of inventory, whereas the pull (lean) system didn't,
- Everyone except the last person was busy in the batch system, whereas people were left waiting for work to do in the pull (lean) system
- The third person in the chain (where the bottleneck occurred) was VERY busy in both cases.
- Both systems put out products at the same rate.
- The green product was way back in process in the batch system.
Productivity
- What did this show about each person's productivity?
- What did we learn about the productivity of the system?
- Are these things different?
- How long did it take to produce a single item from start to finish in each system?
Waste
The batch system generated lots of wasted inventory (products sitting around) and time wasted in work that’s not needed.
How can the process be improved?
- Everyone in the process being constantly busy doesn't tell you anything about the productivity of the whole process.
- If you optimise one part of the process, it doesn't necessarily improve the process as a whole.
Could the process be balanced somehow on a permanent basis?
How would each system respond to unexpected changes...
What if…?
- we wanted to manufacture a different paper shape all of a sudden.
- we increased the batch size to more than one? (would the process be more or less responsive?)
Summary
- Lean flow is a pull system - batch processing is a push system (we're going to make x of these whether we need them or not!)
- Lean helps to identify the constraints of the process by people waiting around (not with stock piling up).
Posted under:
Recent Blogs
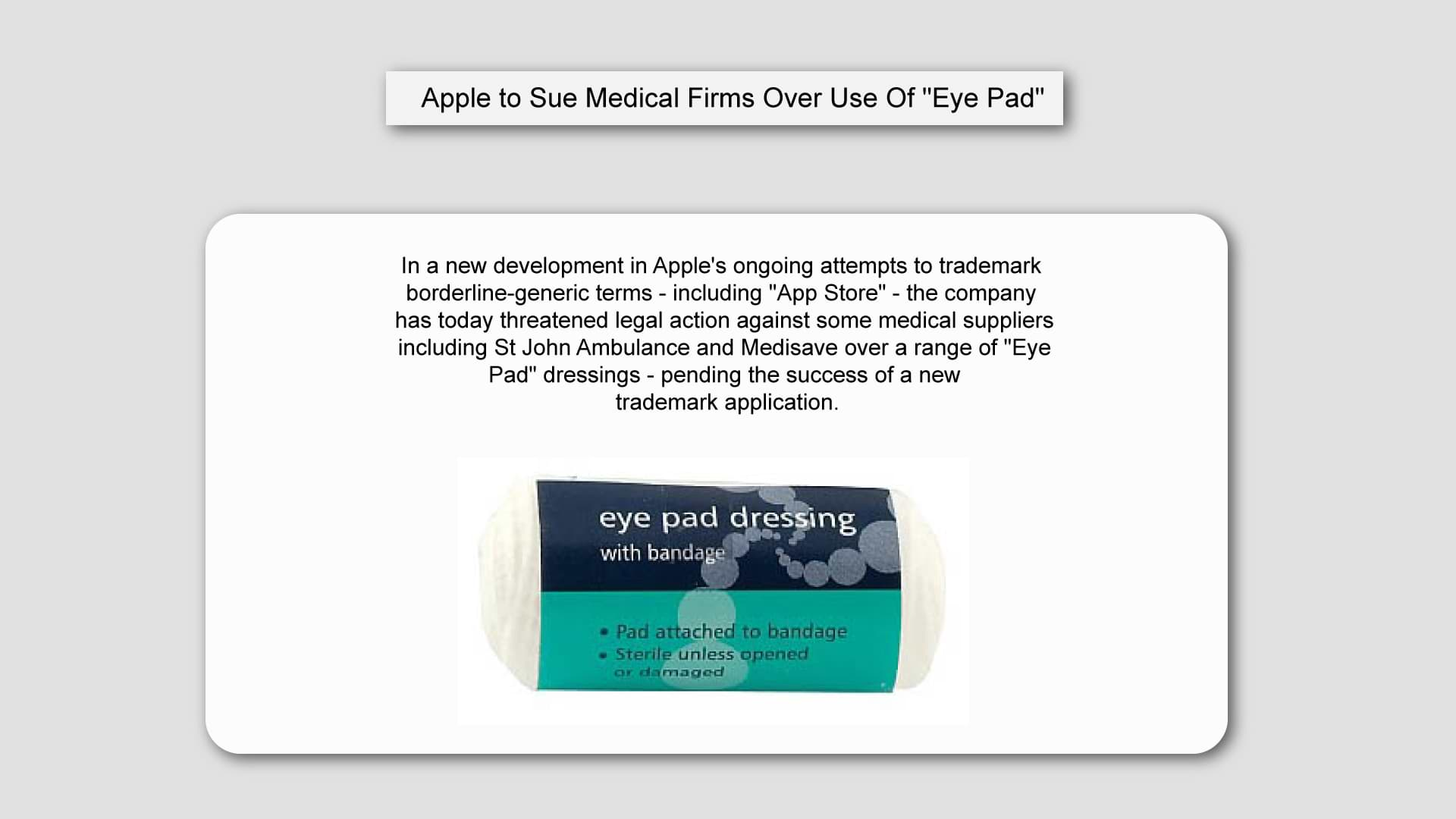
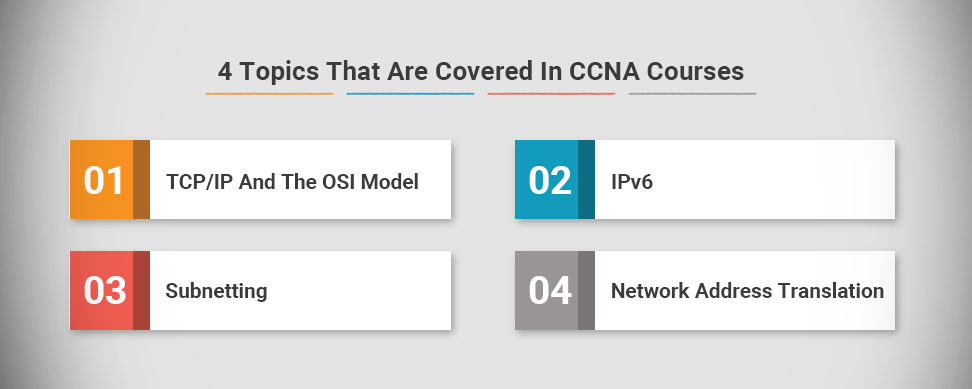
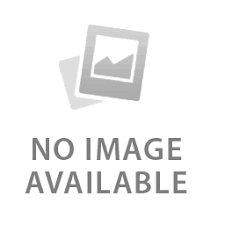