Andy Trainer
16 Oct 2013
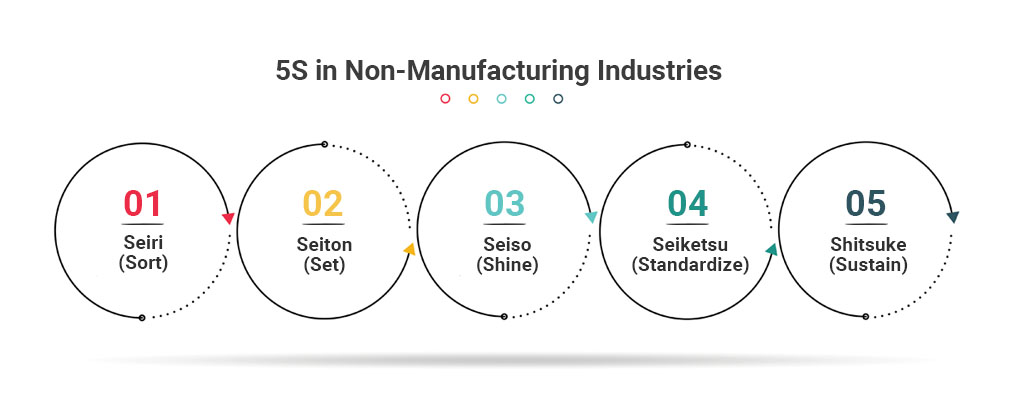
Lean Six Sigma: Using 5S in Non-Manufacturing Industries
Six Sigma was initially developed within the manufacturing industry as a means minimise deficits. Today it is used in all sorts of industries (and there's a high demand for it as a qualification), from healthcare to sales. Our various Six Sigma Courses have been attended by firefighters, insurers and civil servants, just to name a few!
One particular tenet though, 5S, seems rooted in Six Sigma's manufacturing history. How can 5S, an idea coined orginally coined to improve the factory floor, be applied outside of manufacturing?

We asked some experts for their views and received some fantastic feedback. Thanks to all who responded and here's what they had to say.
IT Services
Six Sigma has seen a boom in the IT industry so it makes sense to see 5S being used in some innovative and effective ways:
Operational Excellence Project Manager at Ingersoll Rand
I made significant use of 5S principles in an IT directory services project. The directory itself was Microsoft Active Directory, an LDAP compliant database that holds a large number of types of objects, but the ones I was most interested in were users and computers. Each of these has an account with passwords used for authentication. Seiri: (Sort), I first identified similar objects and similar roles Seiton: (Set), I moved all objects into related Organizational Units (think about it like a folder structure on your hard drive). I organized by object type, then by region, country, and location strong>Seiso: (Shine), I examined the objects and found that many were obsolete (40%+) due to computer replacement or users no longer with the company, so I created some automated scripts to deal with those obsolete objects to clean things up.
Seiketsu: (Standardize), In this stage, I created a role based security model and applied security permissions to the OUs I put the objects in. So if we hire a new desktop engineer, they get added to a single group with all other desktop engineers and they get their rights set in one shot. By using the security principle of least delegation, I built up roles that are standardized. I also set security on the user OUs so that no computer objects can be created there, and vise versa.
Shitsuke: (Sustain), I destroyed the old structures for users and computer objects, so that nobody could go back and use them. I also set up monthly cleanup activities so that a lot of cleanup would take place continuously.
Now, you might think that all of this activity in a virtual world wouldn't pay off in any way, but one of the realities of today's IT world is that a lot of things are outsourced, and in this case email was outsourced. It turned out that many of the accounts that were stale had email provisioned, with a corresponding monthly charge. I'm not going to say how many there were, or what they cost individually, but let's just say I could comfortably live on the savings stream from the project.
There were dozens of other spinoff benefits:
1) Able to easily audit user rights for compliance (PCI/SarbOx,, etc)
2) Simplification of group policy object structure (essentially configuration rules) dropped the total number by 100's
3) Common organization model meant that we could now automate many tasks that were not possible previously.
4) Other systems were simplified - software distribution via SCCM, patch application via WSUS
5) Simplified the user account management processes
6) Simplified the computer account creation process
7) Eliminated the ability to create many types of defects
8) Improved application of anti-virus software and definition updates
That is just a sample.
All of those came essentially out of what was a 5S exercise.
Mission Director at Orsyp
I did kinda the same in a IT projet that was about consolidation of 2 data center to a brand new site.
We applied the 5S before moving any server... Sort out all the stuff, server, cables, racks and so on... We saved around 150 000 € worth of IT asset (about 10% of total budget) by removing old server, balancing under used ones, sorting and putting standard.
We then applied control card to monitor Data Center Capacity.
Racecar Example
This is a great analogy here that makes it easier to understand the usefulness of 5S.
Operational Excellence/Quality Manager
A great teaching example is pit stops in autoracing. Milliseconds can decide who wins.

Public Services e.g. Hospitals and Parks
Public servants from road sweepers to doctors can make use of 5S.
Continuous Improvement Engineer at US Pipe and Foundry
Hospitals do a phenomenal job at 5S. Just as stated above, milliseconds count. Through any organization or business type, each process whether tangible or intangible has a customer external or internal.
For the race car, the driver is the customer and his need is to be back on the track ASAP. Also, the patient at the hospital is the customer.
The next question is: How can I setup my station to best serve my customer? Lean and 5S is much more then a strategy or improvement process. To be truly successful, it needs culture change. That culture change begins with an attitude of servitude towards the customer.
A willingness to change what has been done, change my outlook and change my process to give the customer what they need, when they need it in the amount they need in the time they need it in.
Think of some of your best restaurant or shopping experiences. You will realize that the ones that stand out are the ones with the focus on you, the customer and their 5S efforts are geared towards that end.
Project Team Leader- SSM Health Care, St. Louis
In healthcare, 5S can be very effectively deployed to not only create a well-organized efficient workplace but can promote teamwork and safety in an environment where parallel work is the norm.
5S is a building block that promotes mutual support and while change is always challenging in healthcare it creates something tangible that clinicians can quickly implement and understand how that change made a difference.
Applying lean principles to supply room management then allows healthcare workers the ability to contribute in controlling costs and reduce waste associated with excess inventory and expired items.
Performance Improvement Manager at Skagit Regional Health
Agreeing with Michael. Nowhere is organization and the ability to locate what you need more needed than in an acute care hospital, in the Emergency Department or the Operating Room. Central supply, medication rooms, IS storage, and the print shop, all benefit with 5S application.
Chief Ranger at Metroparks of the Toledo Area
I will be presenting information in December to employees of Michigan State Parks centered on how to apply 5 S in the Parks and Rec sector.
Topics will include how Toledo Area Metroparks was able to apply lean philosophies to their 150 mile trail system, their fleet management processes, and their energy management processes.
Metroparks started with organizing storage rooms and offices, but then catapulted that effort into a culture that utilizes lean philosophies for most of their critical processes.
Sales
A more abstract use of 5S here but one which can have huge benefits in terms of boosting profit.
Management Professional Using LEAN Six Sigma Methodology to Improve Organizations
One aspect you might consider that I am currently working on for a blog of my own is using 5S to "clean" up the sales lead funnel, using the different 5S methods to arrange leads where they should be appropriately located in the sales funnel for an organization - this would give 5S a marketing/sales spin.
Offices and Workspaces
The modern day equivalent of the factory floor, it makes sense for office organisation make use of 5S.
Owner and Principal Consultant for Ott Consulting
The criteria is similar to manufacturing, use the 5S approach, but change the wording, i.e. instead of workbenches to be organized change it to desks and cabinets in an office environment, instead of tooling in mfg. change to project folders, create shadow boards for office supplies at desks, ensure standard work (SW) is in place and job instructions for i.e. nurses to check in patients, or engineers to create BOMs, etc. don't worry too much about creating a perfect 5S document, but create a standard and track and improve from there.
Performance Focused Consulting & Coaching
Anyone's work space can be 5S'ed. However be careful this is personal space and the closer you get the more uncomfortable the owner/user of that space can become.
Example: If you observe the workers in a call center for several days as they take calls, answered questions, solve problems, placed orders, etc. You would see how they use their tools (PC, Phone, Staplers, Pens, Reference Manuals, Catalogs, and their space (Desk Top, Overhead Cabinets, file drawers, etc.) You would see/find wasted movements, cluttered drawers, overstocked office supplies, missing tools.

The 5S process could help you improve efficiency and productivity by optimizing the space and making sure the right resources, are in the right place, and in the right quantity. If the work space is shared by other Phone Associates working other shifts you certainly would see improvement when everything has a place.
Expand this to include the entire office area and you would see similar opportunities for the positioning and usage of fax machines, file cabinets, office supplies, mail room, even proximity to key support departments.
APAC Regional Director Support Services at JDA Software
Some good ideas above.
How about some small stuff
- De-clutter your desk, and that doesn't just mean dump all the stuff in your drawers out of sight.
- De-clutter your desktop home screen. While doing this, organise your folders so you can find all your saved documents quickly
- Organise your Outlook into folders that make sense and make retrieval easy.
- Scan paper docs you don't need hard copies of and store electronically
- Actually put all your regular scheduled meetings into your calendar along with any necessary prep time. While you are at it, schedule going home time.
- Simplify your writing. Core idea up front. Keep your sentences short by using less commas and ands.
Founder and Host at StatStuff
I think that in any business area that is a space either shared by multiple people or where a repeatable process is performed can benefit from 5S.
For non-manufacturing shared spaces, some examples include office cubicles that are shared by multiple workers such as for those who are remote employees visiting their home office or phone reps at a call center.
I think this could be extended to include community office spaces such as when they have a shared copier or printer and want to have some of the related tools accessible to workers (like stapler, scissors, cutter, pens/paper, etc.).
For repeatable processes, this could include any person who has a permanent location for performing their work such as folks in a billing department preparing customer bills, a mailroom, a finance department producing monthly financial docs, etc.
But I think someone can even apply this virtually to some degree to their own minds - that is, by applying 5S to our own thoughts, vision or plans can help ensure we're operating more efficiently and keeping the right priority of things.
Everything(!)
5S is applicaple to just about every area of business and life.
Principal Consultant
Easy - if you understand that the fundamentals and ignore the mechanistic approach proffered by those who consult based upon what they have read in a book as opposed to what they have learnt in practice.
The true message behind the 5S's is one of efficient and productive working practice. They simply define the basic operating DNA of an excellent operation and it's culture - regardless of business sector.
Lead Mechanical Engineer
Every thing we do, use in our day to day life can be brought under 5S. Like for example, security system, parking space, space we eat, space we work, space we meet in conference room, the way we organize meeting, mails, contacts, list will keep coming.....it's never ending....
Credit to Flavio Martins for main image.
Posted under:
Recent Blogs
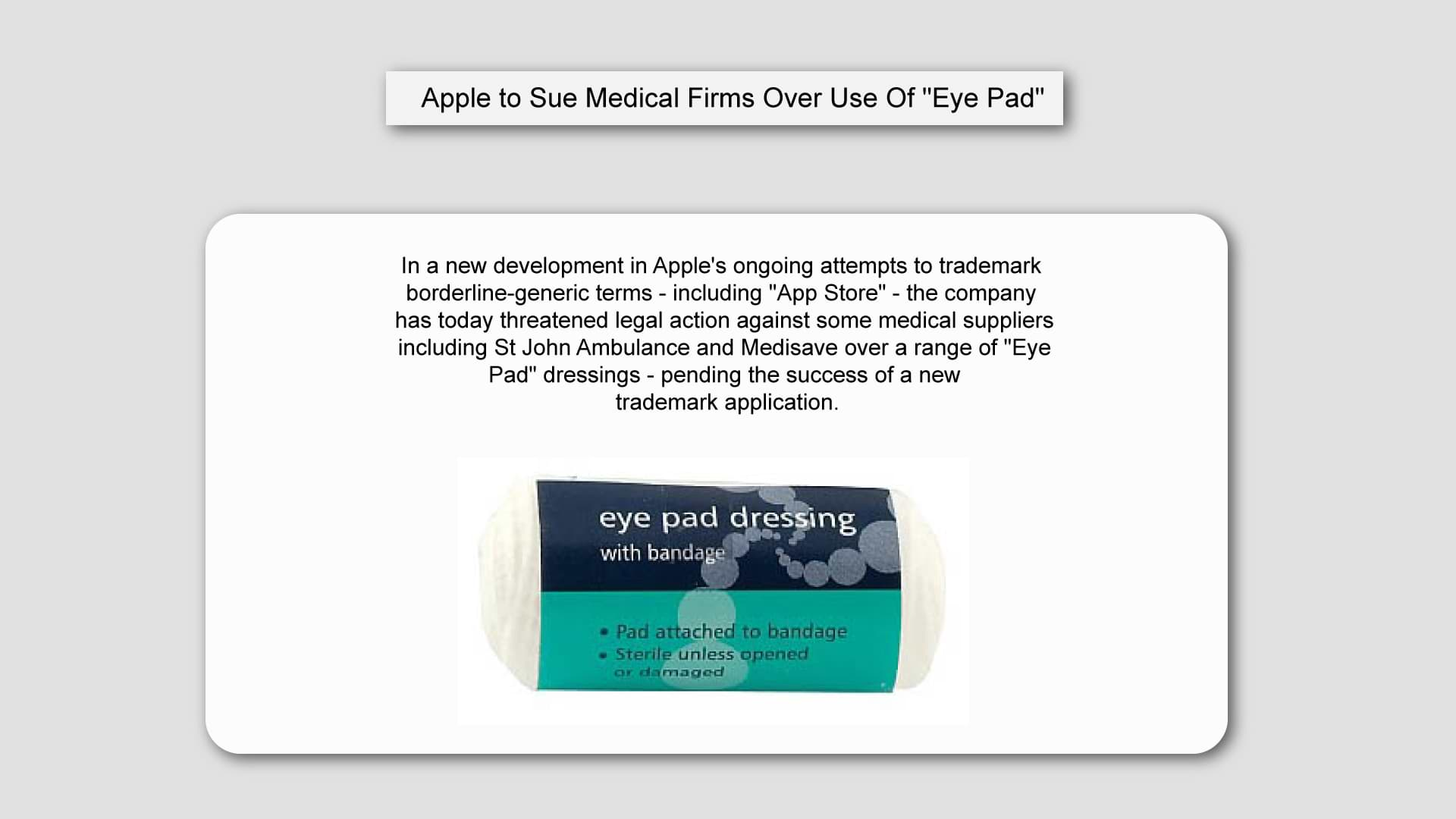
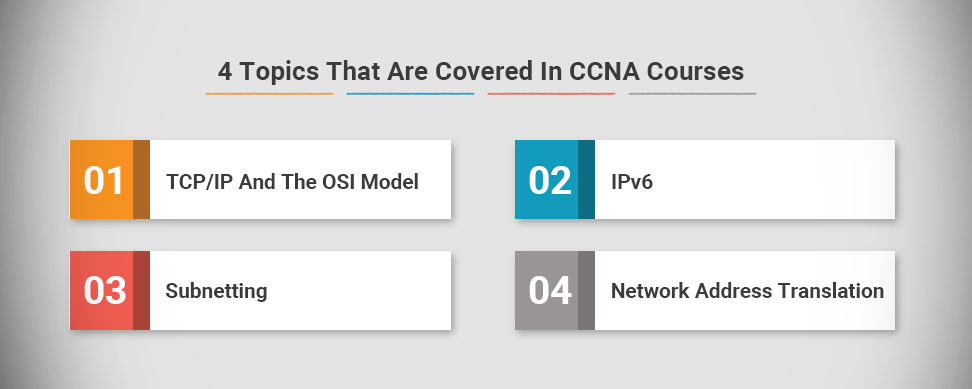
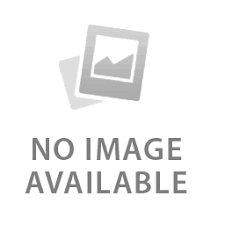