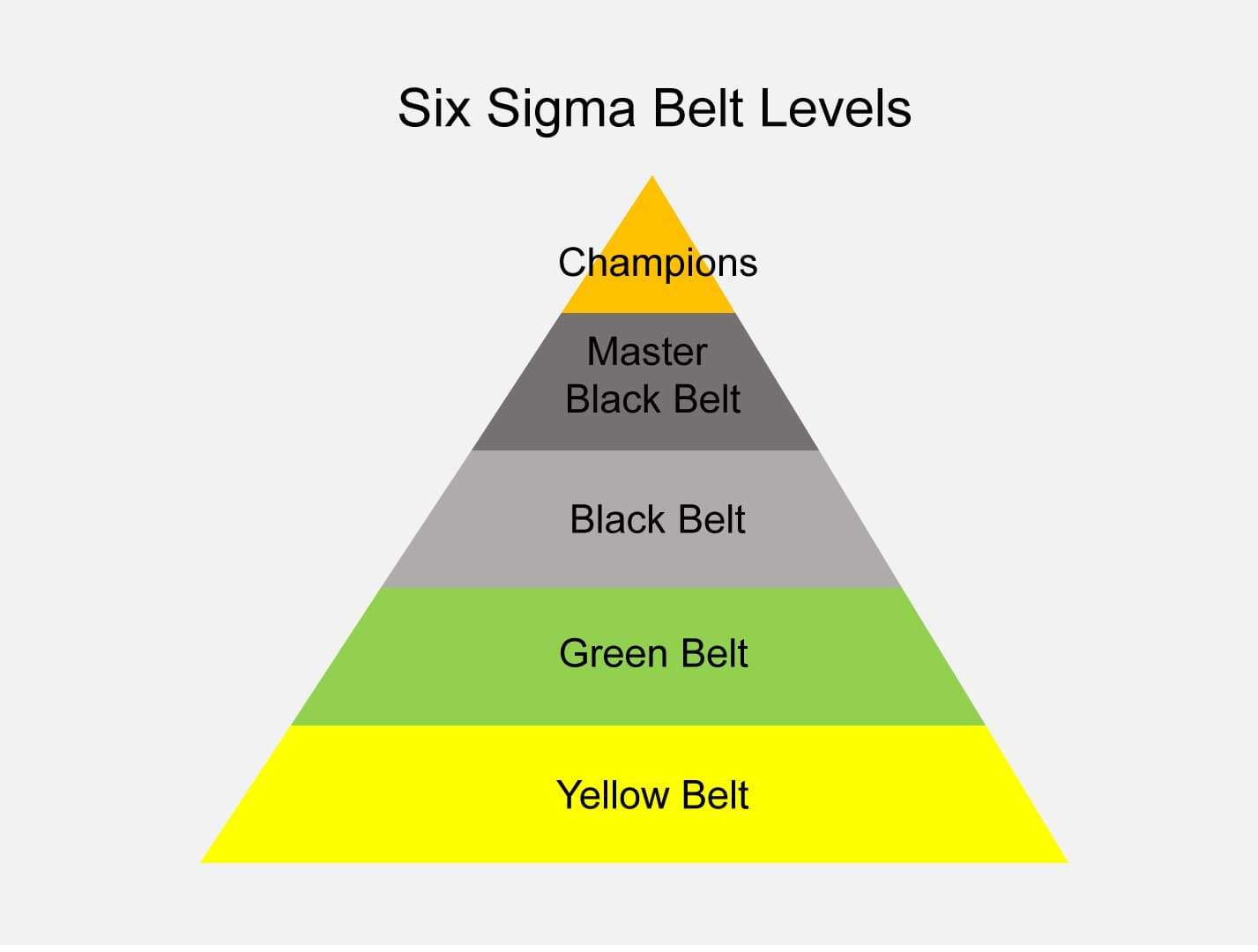
Green Belts and Black Belts? Similar to martial arts, Lean Six Sigma uses a coloured belt ranking terminology to define the level and function of Six Sigma practitioners.
But what do the levels mean?
In this guide I'm going to run through the Six Sigma belt levels to explain their role and function and how you can achieve each level.
This should help you when deciding what level of Lean Six Sigma Training different team members require to successfully run Lean Six Sigma projects.
To learn more about Six Sigma including the Belt levels, download our free eBook 'What is Six Sigma?'
Lean Six Sigma Yellow Belt
Yellow Belts are team members on Six Sigma projects. They need to understand the key processes and some of the basic Lean Six Sigma tools to work on a project but not to the level of Green Belt.
We run a 2-day Lean Six Sigma Yellow Belt course to enable Six Sigma team members to improve their understanding and awareness of Lean Six Sigma tools and processes.
Training team members to Yellow Belt level improves performance and reduces timescales on Six Sigma projects.
Andy Trainer
9 Jan 2014
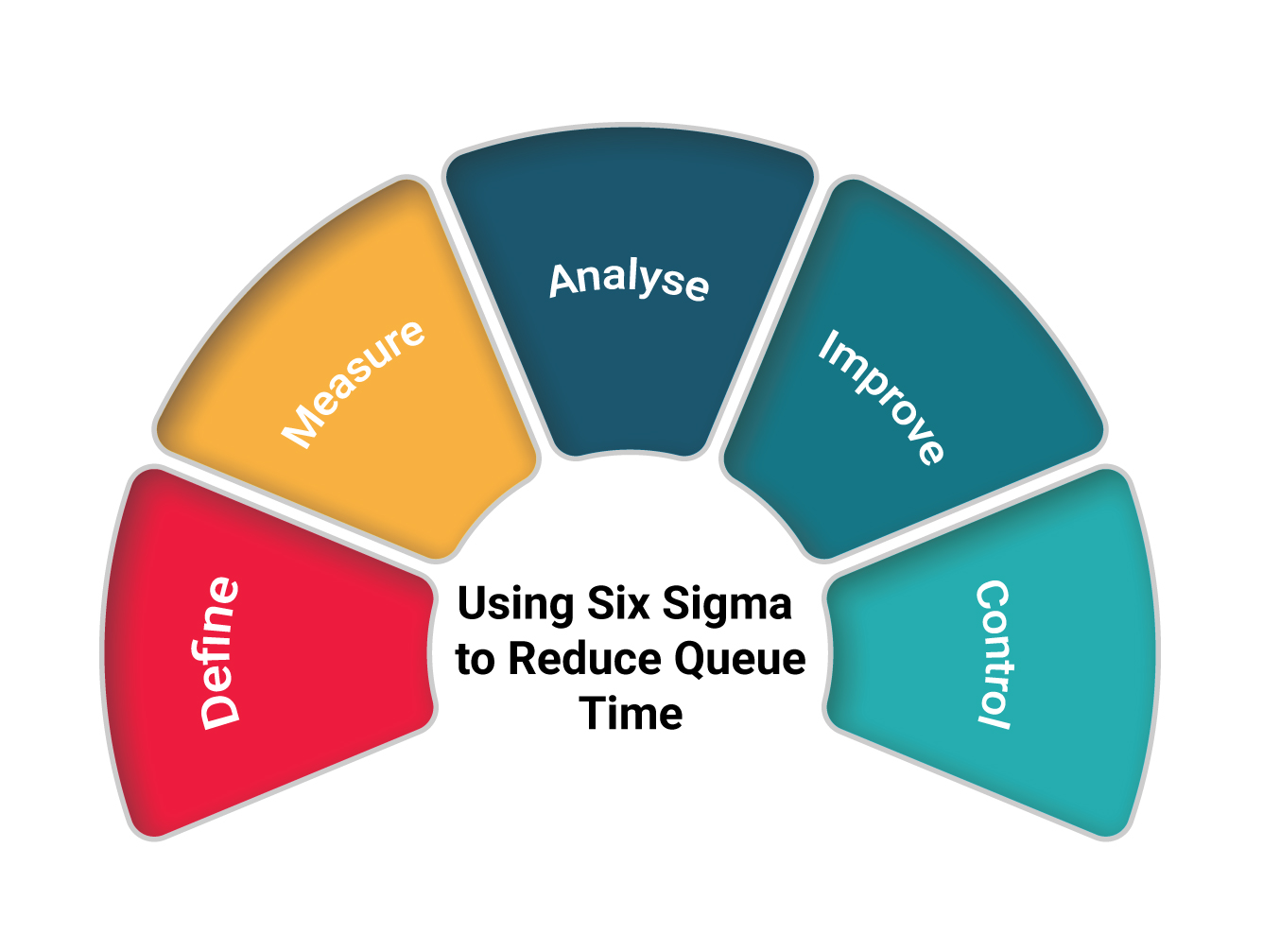
Everyone hates queueing. It annoys customers and business-owners alike; so much so in fact that queue management is considered a significant part of business theory as it can have a huge impact on the service that a customer receives.
If it's done well, it becomes a barely noticeable aspect of the experience. Done wrong, and it can lead to excessive waiting times that will distress and irritate the customer.
Using the DMAIC method from Six Sigma, it's possible to reduce waiting times in queues for everywhere from supermarkets to airports. This will lead to a better service overall and that means happy customers.
Six Sigma is used in a wide variety of businesses and settings to increase efficiency and quality. From factories to governments, its primary use is to make processes better. On our Six Sigma Green Belt Training Course you'll learn all the basics of how to apply Six Sigma to your business needs.
Define
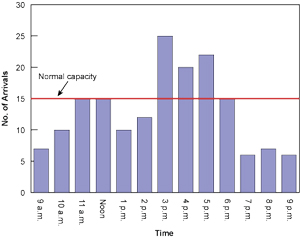
So firstly, it's important to define what the exact issue is with the queueing system. Is it that the waiting time is consistently so long that customers are actually leaving before reaching the front? Is it that there are certain 'peak' times when staff can't handle the volume of customers?
Knowing exactly what the problem is allows for more targeted, and therefore successful, addressing of the issue.
According to queue management theory, there are three aspects of queueing which could be causing an issue:
- Arrival Process
- Service Mechanism
- Queue Characteristics
Arrival Process
How is it that customers are coming to be in the queue? Do they arrive in droves? One-by-one? Is there a primary queue and a secondary queue (like at a club for example; one queue to get in, another to pay)?
Is there some kind of bottleneck in the arrival process that means too many customers enter the queue at once? Answering these questions allows you to pinpoint the problem if it's in the arrival process.
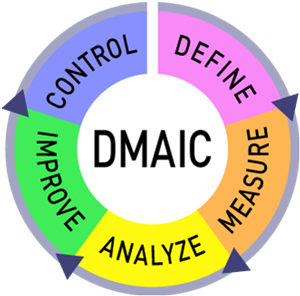
Andy Trainer
7 Jun 2013
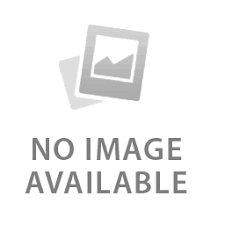
What is the most effective way of improving my organisation?
Why does your organisation exist?
If it’s a commercial company, you want to make profits. If you are public sector or charity, then you want to apply your resources to best effect for your users.
Your business may be manufacturing (making widgets), information-processing (“transactional” such as finance and design) or service industry such as travel & transport, distribution, holidays and hotels. To make money (profit) you need to havefast and efficientthroughput of work from the start of the process to the customer.
What is Lean Six Sigma?
To improve flow of work and drive out waste (waste is anything you do that your customers won’t be happy paying for) many organisations use the highly effective tools of lean thinking. To reduce unwanted variation causing waste and troubling the customer we can use Six Sigma which is a powerful statistical toolkit. The combination of lean thinking and Six Sigma is Lean Six Sigma: widely and successfully used in very many organisations. Good training is available: for example, Silicon Beach Training offerLean Training&as well asSix SigmaYellow Belt(three days),Green Belt(five days) andBlack Belt Conversion(additional ten days).
Andy Trainer
13 Jun 2012
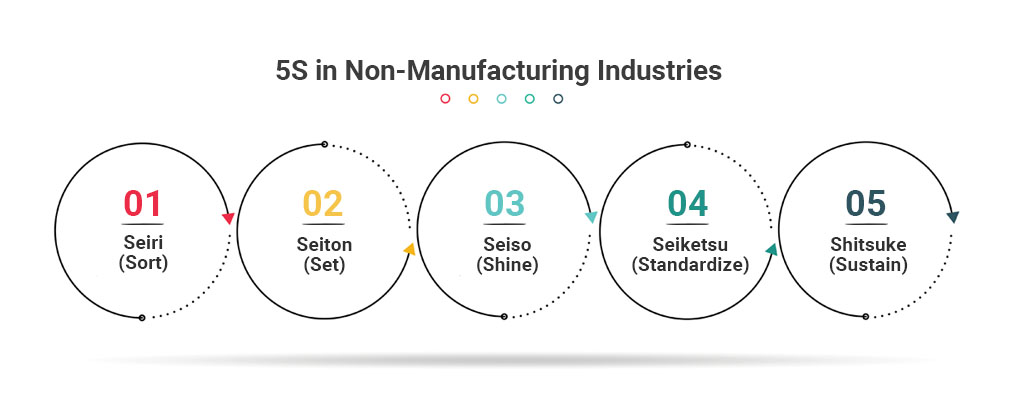
Six Sigma was initially developed within the manufacturing industry as a means minimise deficits. Today it is used in all sorts of industries (and there's a high demand for it as a qualification), from healthcare to sales. Our various Six Sigma Courses have been attended by firefighters, insurers and civil servants, just to name a few!
One particular tenet though, 5S, seems rooted in Six Sigma's manufacturing history. How can 5S, an idea coined orginally coined to improve the factory floor, be applied outside of manufacturing?
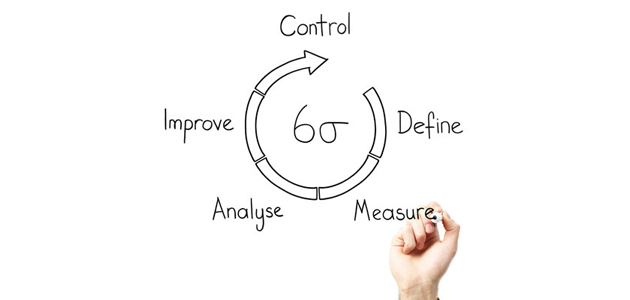
We asked some experts for their views and received some fantastic feedback. Thanks to all who responded and here's what they had to say.
Andy Trainer
16 Oct 2013
Recent Blogs
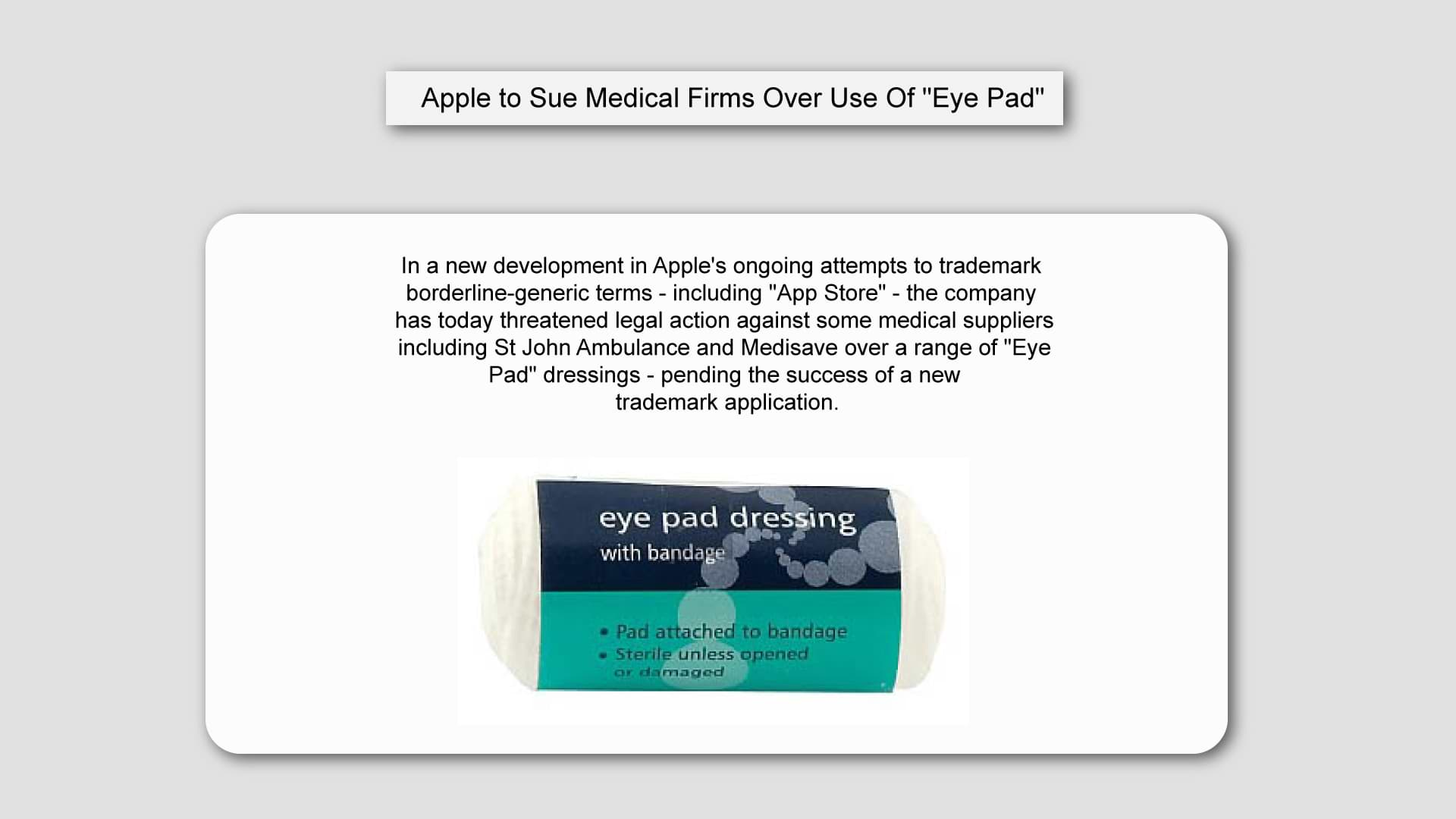
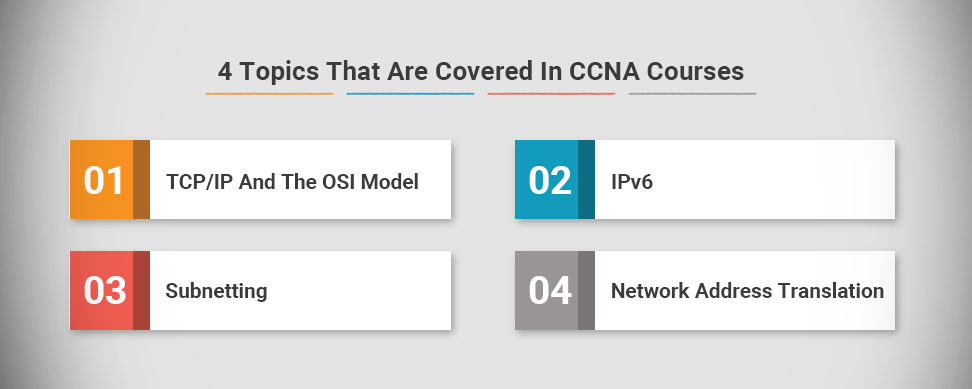
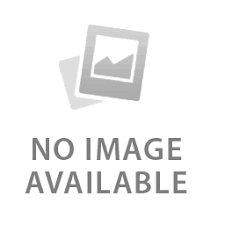
