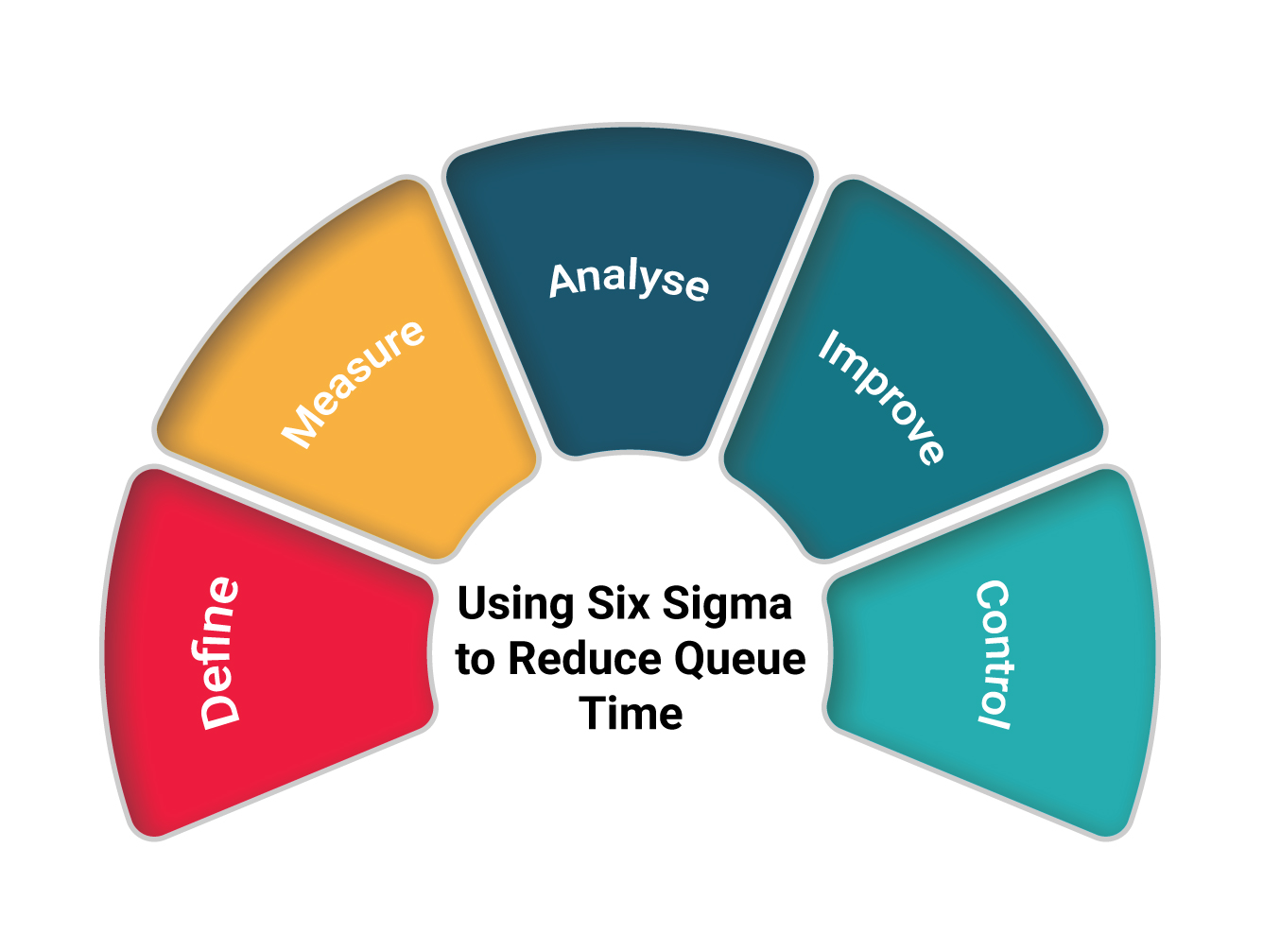
Everyone hates queueing. It annoys customers and business-owners alike; so much so in fact that queue management is considered a significant part of business theory as it can have a huge impact on the service that a customer receives.
If it's done well, it becomes a barely noticeable aspect of the experience. Done wrong, and it can lead to excessive waiting times that will distress and irritate the customer.
Using the DMAIC method from Six Sigma, it's possible to reduce waiting times in queues for everywhere from supermarkets to airports. This will lead to a better service overall and that means happy customers.
Six Sigma is used in a wide variety of businesses and settings to increase efficiency and quality. From factories to governments, its primary use is to make processes better. On our Six Sigma Green Belt Training Course you'll learn all the basics of how to apply Six Sigma to your business needs.
Define
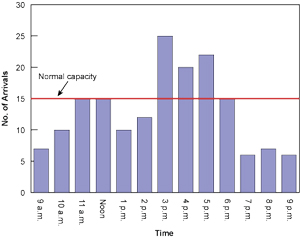
So firstly, it's important to define what the exact issue is with the queueing system. Is it that the waiting time is consistently so long that customers are actually leaving before reaching the front? Is it that there are certain 'peak' times when staff can't handle the volume of customers?
Knowing exactly what the problem is allows for more targeted, and therefore successful, addressing of the issue.
According to queue management theory, there are three aspects of queueing which could be causing an issue:
- Arrival Process
- Service Mechanism
- Queue Characteristics
Arrival Process
How is it that customers are coming to be in the queue? Do they arrive in droves? One-by-one? Is there a primary queue and a secondary queue (like at a club for example; one queue to get in, another to pay)?
Is there some kind of bottleneck in the arrival process that means too many customers enter the queue at once? Answering these questions allows you to pinpoint the problem if it's in the arrival process.
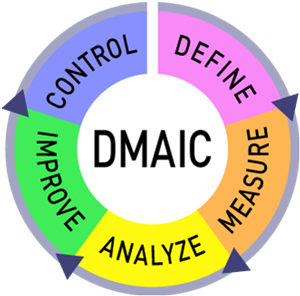
Andy Trainer
7 Jun 2013
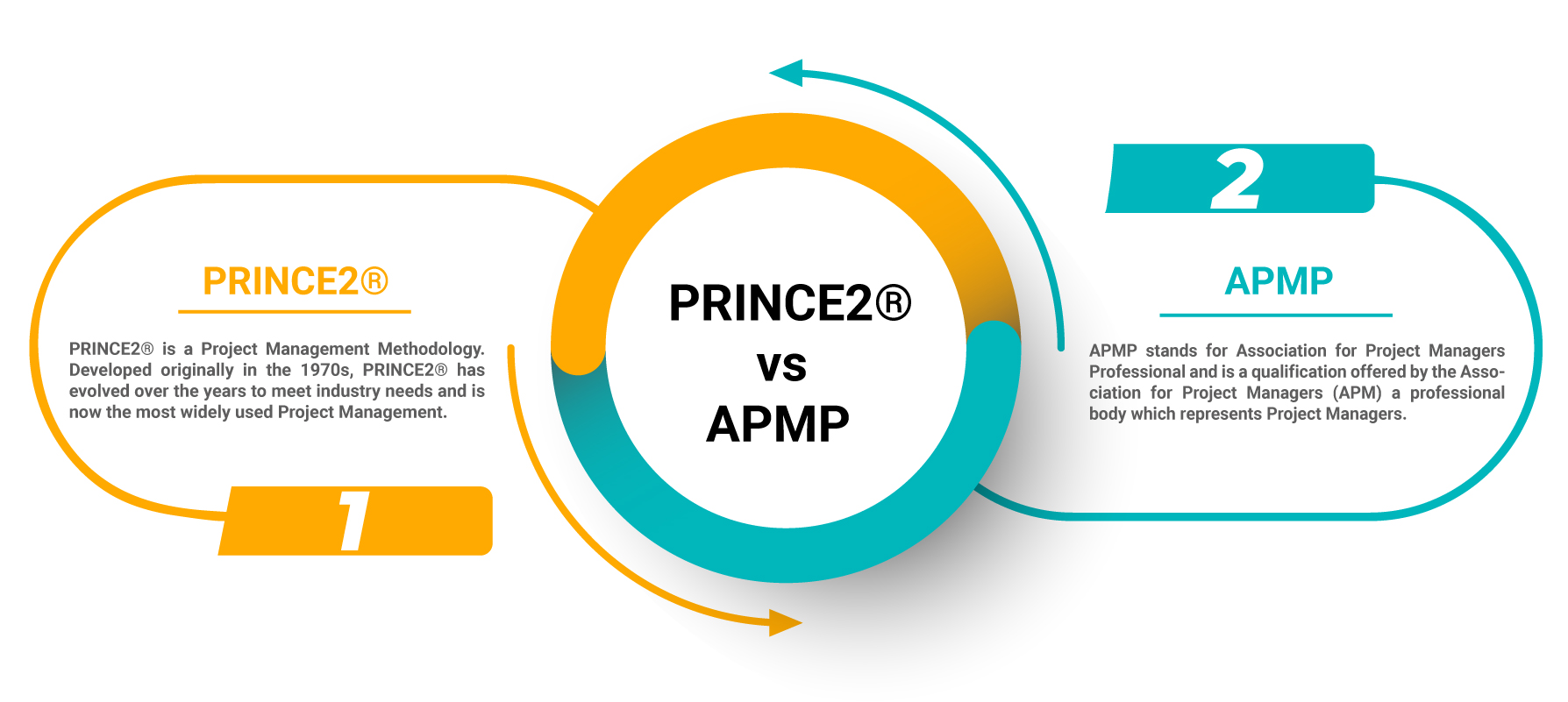
We do a lot of project management training here at Silicon Beach - including our most popular PRINCE2® courses - and we're often asked: "should I take the PRINCE2® Practitioner or the APMP qualification?"
There are some important differences between PRINCE2® Practitioner and the APMP qualification, and we'll cover those as quickly and clearly as we can here.
Andy Trainer
14 Jul 2010

PRINCE2® PROCESSES – Managing Product Delivery (MP)
The purpose of the Managing Product Delivery process is to control the link between the Project Manager and the Team Manager(s), by placing formal requirements on accepting, executing and delivering project work.
The role of the Team Manager(s) is to coordinate an area of work that will deliver one or more of the project’s products. They can be internal or external to the customer’s organisation.
The objective of the Managing Product Delivery process is to ensure that:
- Work on products allocated to the team is authorised and agreed.
- Team Managers, team members and suppliers are clear as to what is to be produced and what is the expected effort, cost or timescales.
- The planned products are delivered to expectations and within tolerance.
- Accurate progress information is provided to the Project Manager at an agreed frequency to ensure that expectations are managed.
Products that are created or updated during this process are:
- Team plans with actual dates.
- Risk register with any identified work package level risks.
- Quality register with all quality work that is being undertaken.
- Configuration Item Records with the latest status of products produced.
- Project Issues with status information and impact analysis for current or new issues identified.
- Checkpoint Reports providing regular progress information to the Project Manager.
Silicon Beach Training is an accredited training organisation for PRINCE2 Training.
Andy Trainer
12 Jul 2007
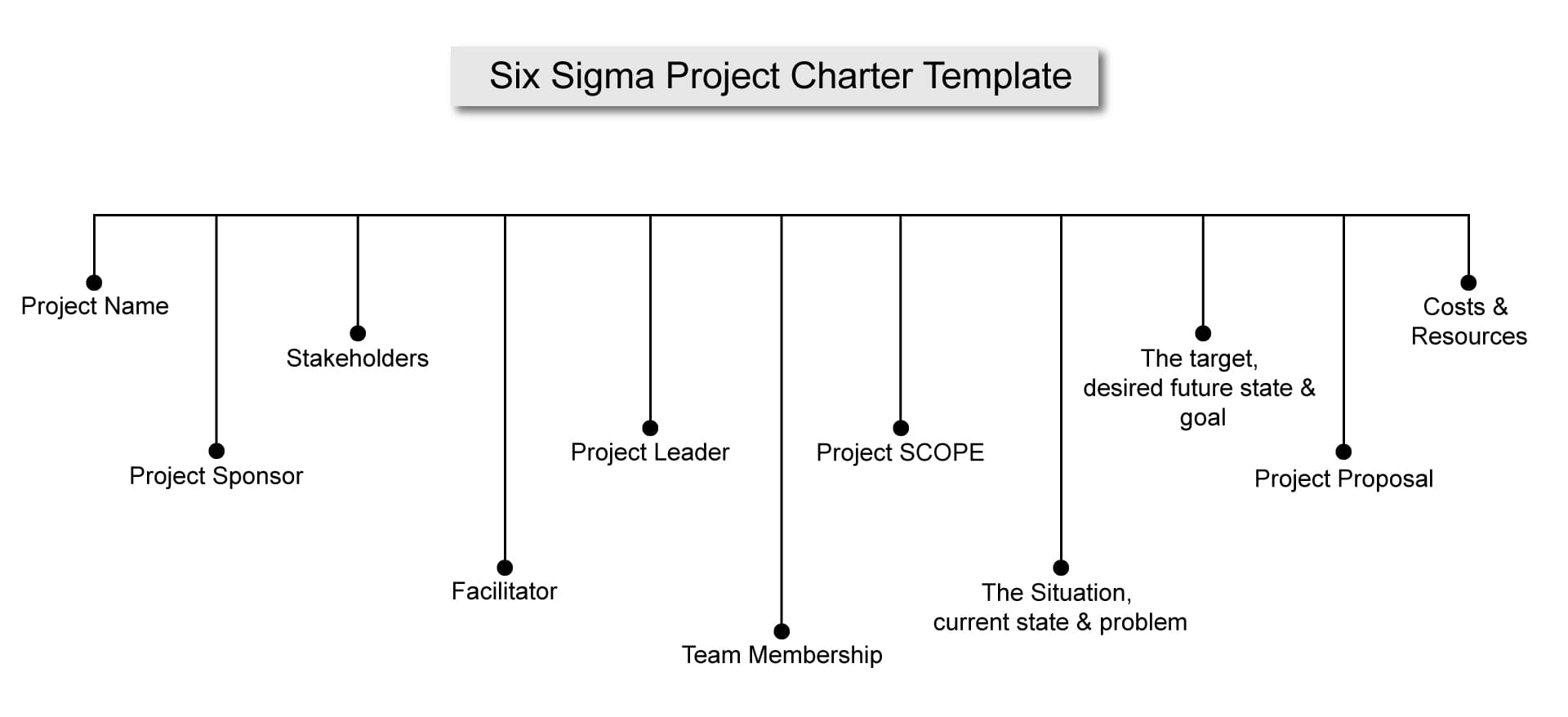
Having a clearly defined Project Charter at the start of your Six Sigma project is one of the key factors for success. A Six Sigma Project Charter defines the purpose and scope of the Six Sigma project and helps to make sure that the project is seen successfully to completion.
The Project Charter is completed during the Define Stage of the Six Sigma DMAIC process. Our range of Six Sigma Trainingcourses covers DMAIC in depth. Check out our Six Sigma Green Belt Training and Six Sigma Black Belt Training courses.
And to help you get up and running quickly you can download our free Six Sigma Project charter using the link above, or by clicking on the image to the right.
DOWNLOAD FREE SIX SIGMA PROJECT CHARTER TEMPLATE
The Six Sigma Project Charter defines:
- Project Name
- Project Sponsor
- Stakeholders
- Facilitator
- Project Leader
- Team Membership
- Project SCOPE
- The Situation, current state & problem
- The target, desired future state & goal
- Project Proposal
- Costs & Resources
- Benefits & Measures
- Project Plan outline
- Risks
- Interrelationships with other projects
Andy Trainer
17 Feb 2011
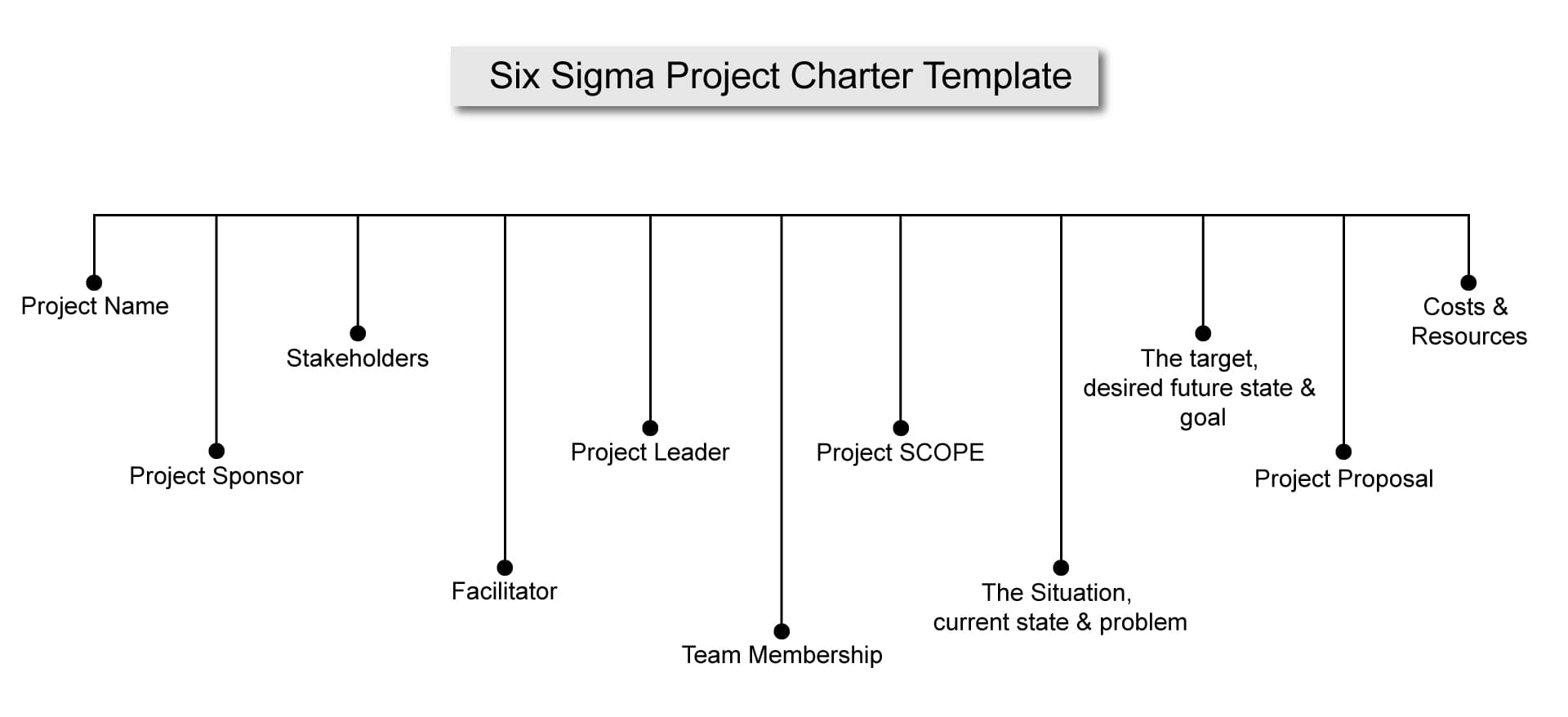
Having a clearly defined Project Charter at the start of your Six Sigma project is one of the key factors for success. A Six Sigma Project Charter defines the purpose and scope of the Six Sigma project and helps to make sure that the project is seen successfully to completion.
The Project Charter is completed during the Define Stage of the Six Sigma DMAIC process. Our range of Six Sigma Trainingcourses covers DMAIC in depth. Check out our Six Sigma Green Belt Training and Six Sigma Black Belt Training courses.
And to help you get up and running quickly you can download our free Six Sigma Project charter using the link above, or by clicking on the image to the right.
DOWNLOAD FREE SIX SIGMA PROJECT CHARTER TEMPLATE
The Six Sigma Project Charter defines:
- Project Name
- Project Sponsor
- Stakeholders
- Facilitator
- Project Leader
- Team Membership
- Project SCOPE
- The Situation, current state & problem
- The target, desired future state & goal
- Project Proposal
- Costs & Resources
- Benefits & Measures
- Project Plan outline
- Risks
- Interrelationships with other projects
Andy Trainer
17 Feb 2011
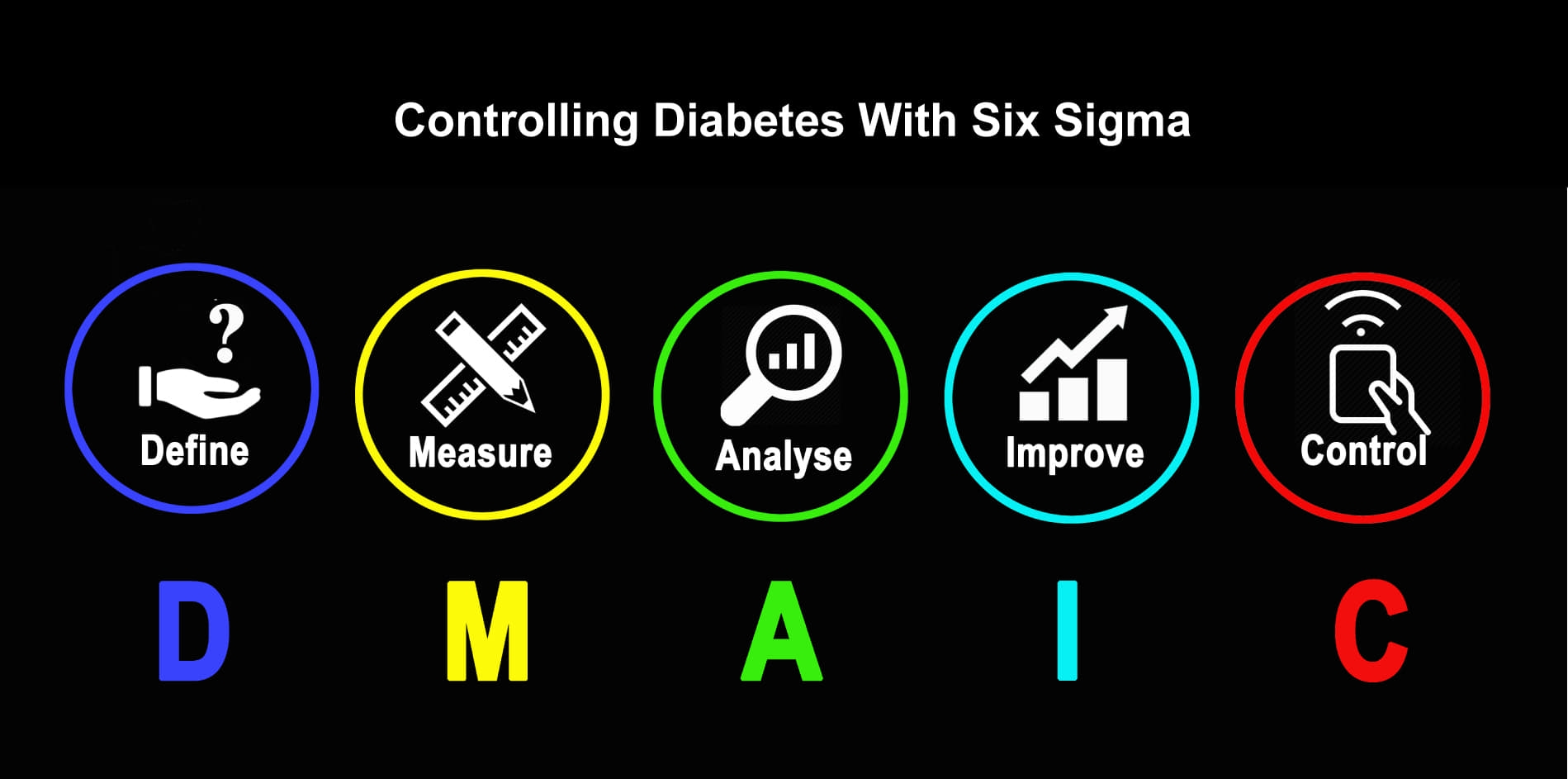
An American man who was diagnose with diabetes used his experience with Six Sigma to control the disease.
William Howell discovered he had Type 2 diabetes and was understandably concerned - potential health risks from diabetes if left unmanaged include blindness, strokes and heart-attacks.
However, William was a Quality professional and was aware of Six Sigma's framework for removing defects. By viewing his undesired symptoms as defects, he was able to use Six Sigma to bring his diabetes under control. You can read excerpts from William's bookabout managing diabetes here.
If you want to learn more about Six Sigma, try our Six Sigma Training.
DMAIC Phases
Howell decided to divide his diabetes plan into the five DMAIC stages -define, measure, analyse, improve and control.
If you want to find out more about DMAIC and other Six Sigma terms, why not download our Lean Six Sigma Glossary.
This is how he used each stage of DMAIC to manage his illness:
- Define Howell created a goal statement. His symptoms were related to his high blood glucose level, so this was the first target - reduce the level to a healthier 125mg/dl or less. His other main goal was to control his symptoms naturally rather than continuing to depend on medication by improving his diet and exercising more.
- Measure- Howell continuously measured his blood glucose levels and charted his food intake, including calories, fat and sugar.
- Analyse- He would then analyse this data for trends - noticing any correspondence between a day of high-calorie intake and high glucose levels, for example.
- Improve- Using his charts, he was able to notice any areas that he could improve upon to further his chance of achieving his goals. If his biggest contributor to high blood glucose levels was the days when he ate doughnuts, for example, his chart would reflect this and he could make the appropriate alterations to his lifestyle.
- Control - By being completely aware of any changes and reasons for them, Howell was able to make constructive choices with the help of his doctor. Any aspects which were causing difficulty could be easily identified and addressed quickly.
Andy Trainer
11 Dec 2012
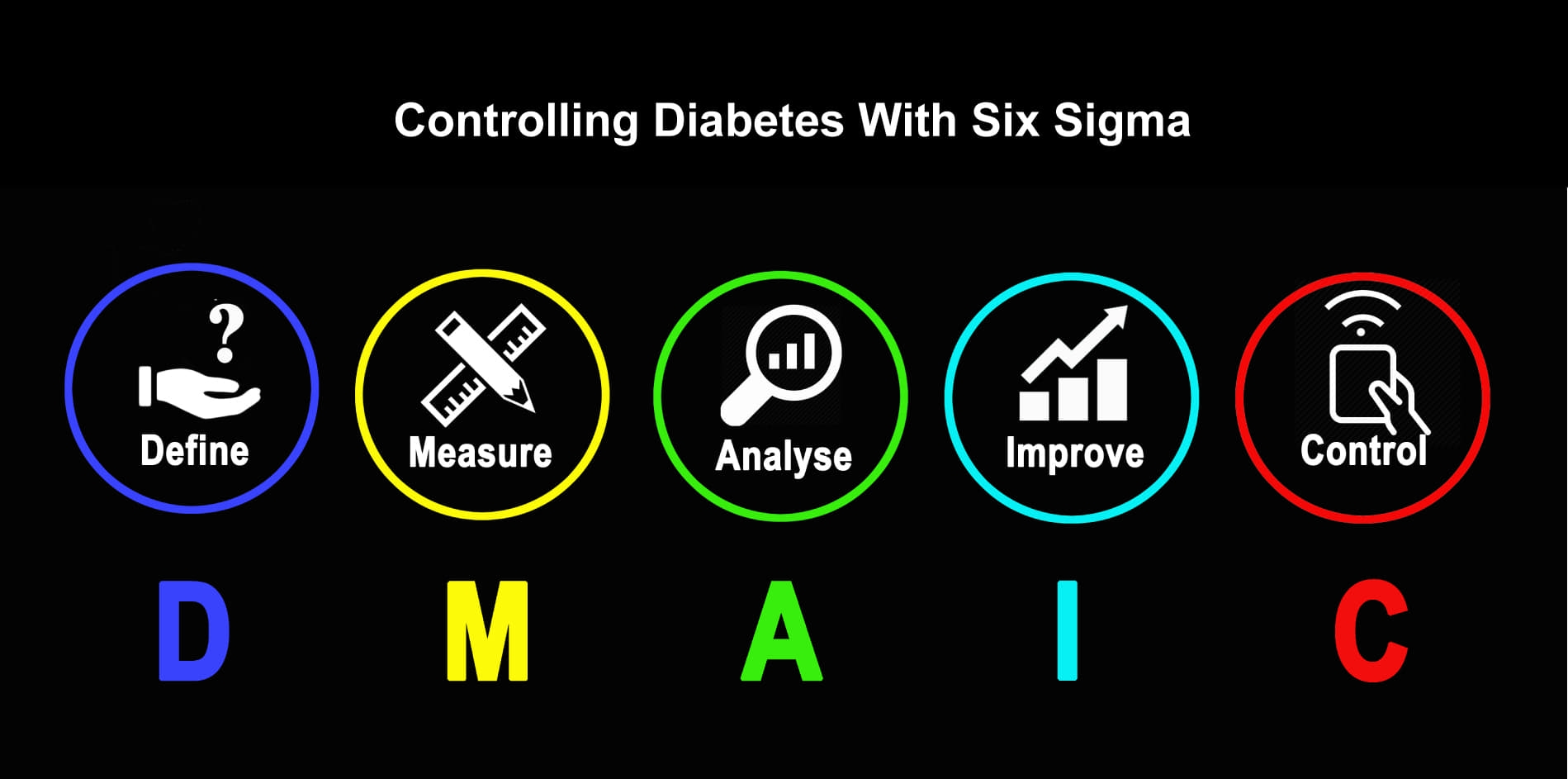
An American man who was diagnose with diabetes used his experience with Six Sigma to control the disease.
William Howell discovered he had Type 2 diabetes and was understandably concerned - potential health risks from diabetes if left unmanaged include blindness, strokes and heart-attacks.
However, William was a Quality professional and was aware of Six Sigma's framework for removing defects. By viewing his undesired symptoms as defects, he was able to use Six Sigma to bring his diabetes under control. You can read excerpts from William's bookabout managing diabetes here.
If you want to learn more about Six Sigma, try our Six Sigma Training.
DMAIC Phases
Howell decided to divide his diabetes plan into the five DMAIC stages -define, measure, analyse, improve and control.
If you want to find out more about DMAIC and other Six Sigma terms, why not download our Lean Six Sigma Glossary.
This is how he used each stage of DMAIC to manage his illness:
- Define Howell created a goal statement. His symptoms were related to his high blood glucose level, so this was the first target - reduce the level to a healthier 125mg/dl or less. His other main goal was to control his symptoms naturally rather than continuing to depend on medication by improving his diet and exercising more.
- Measure- Howell continuously measured his blood glucose levels and charted his food intake, including calories, fat and sugar.
- Analyse- He would then analyse this data for trends - noticing any correspondence between a day of high-calorie intake and high glucose levels, for example.
- Improve- Using his charts, he was able to notice any areas that he could improve upon to further his chance of achieving his goals. If his biggest contributor to high blood glucose levels was the days when he ate doughnuts, for example, his chart would reflect this and he could make the appropriate alterations to his lifestyle.
- Control - By being completely aware of any changes and reasons for them, Howell was able to make constructive choices with the help of his doctor. Any aspects which were causing difficulty could be easily identified and addressed quickly.
Andy Trainer
11 Dec 2012
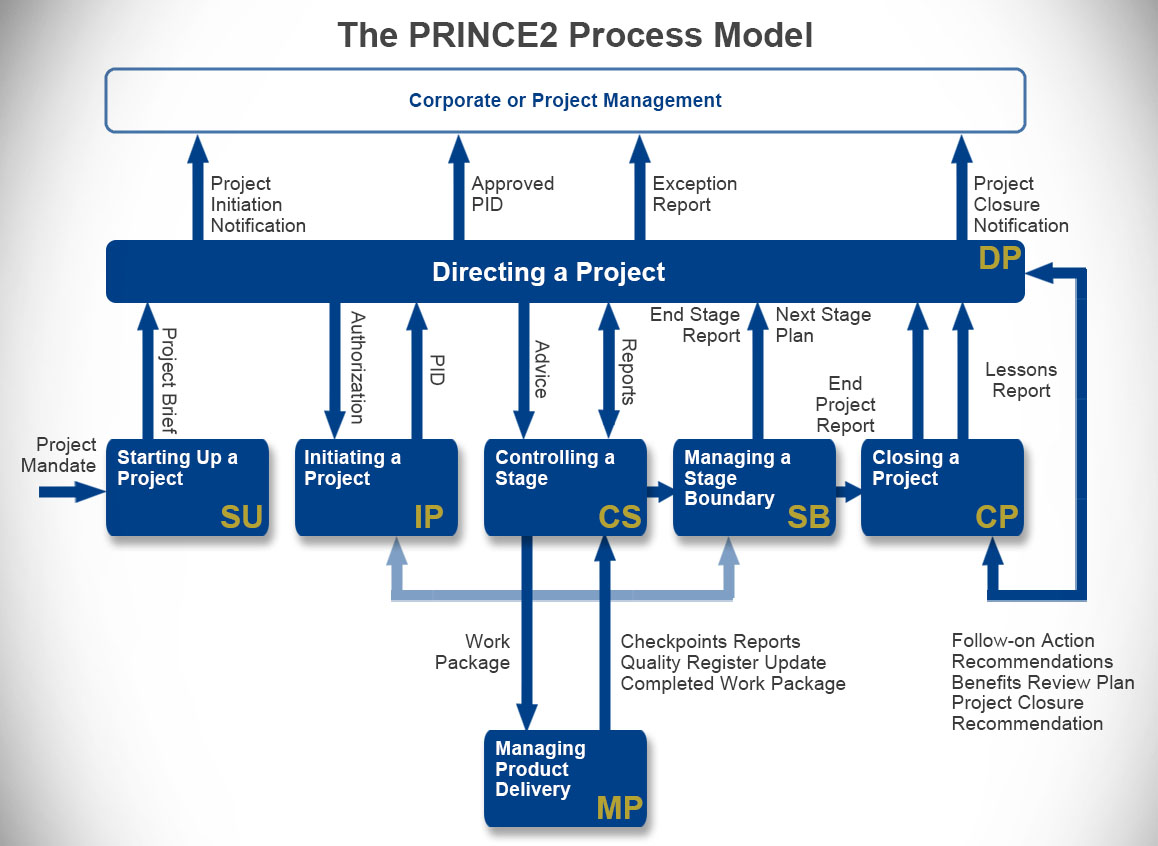
The PRINCE2® Process Model describes the seven processes in PRINCE2 Project Management - click the image to open a larger version in a new window.
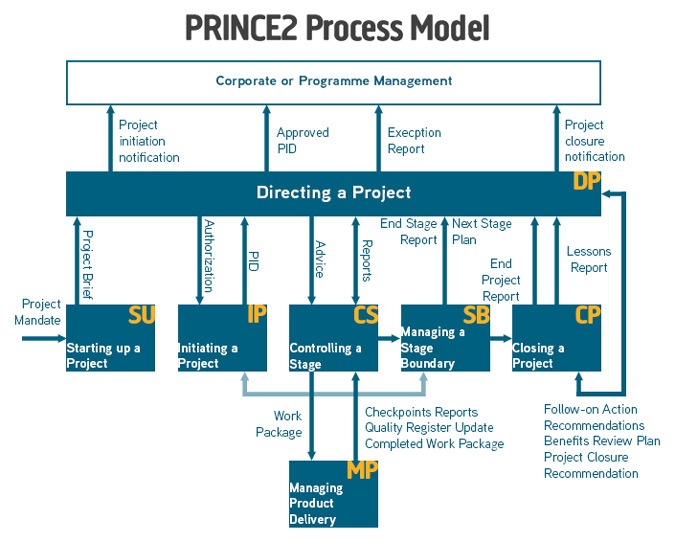
To dig further into the PRINCE2 Process Model and the seven process models, read our article on PRINCE2 Process Diagrams.
Lean more about the PRINCE2 Process Model on our PRINCE2 Courses.
Andy Trainer
16 Oct 2007
Recent Blogs
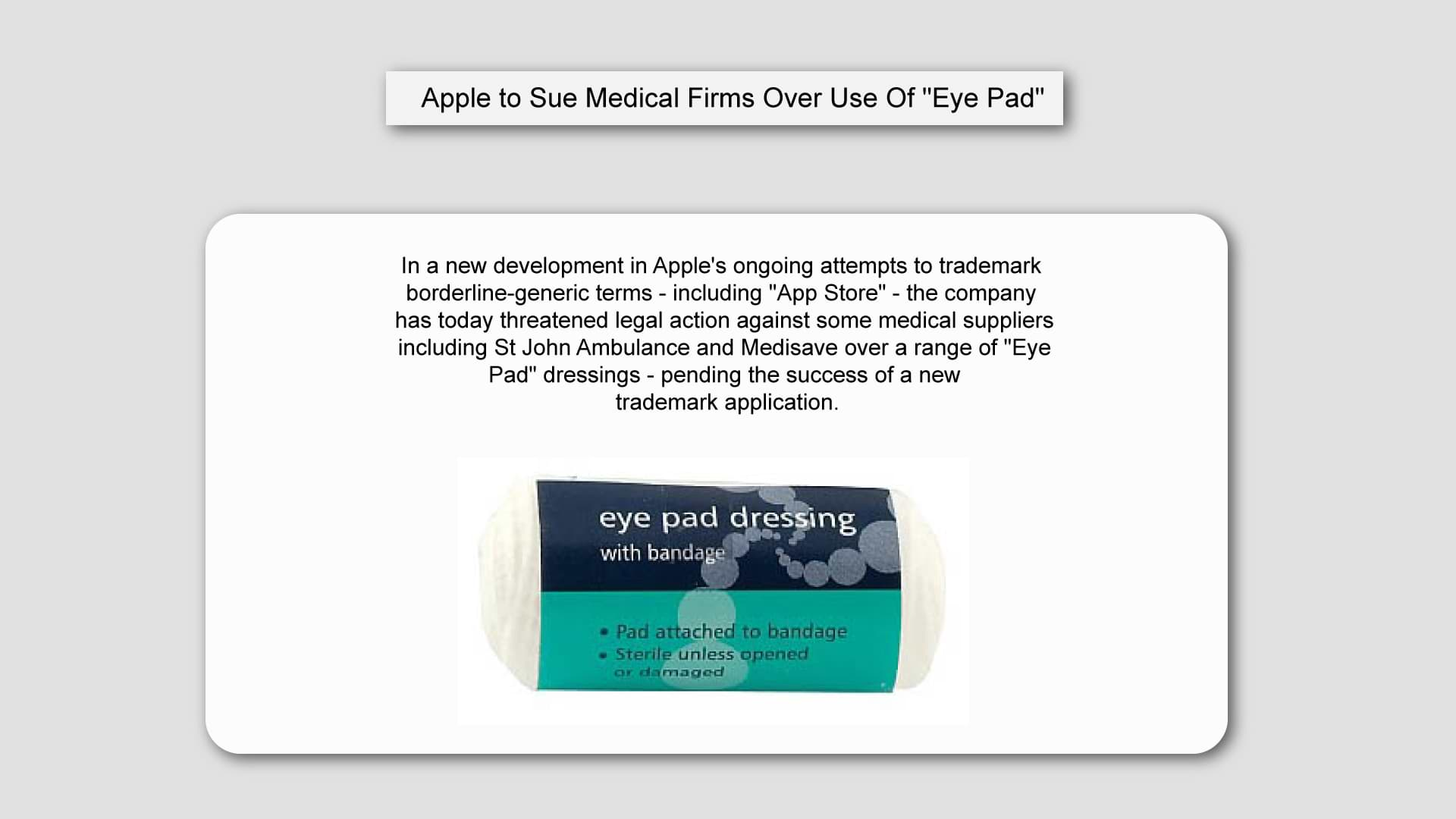
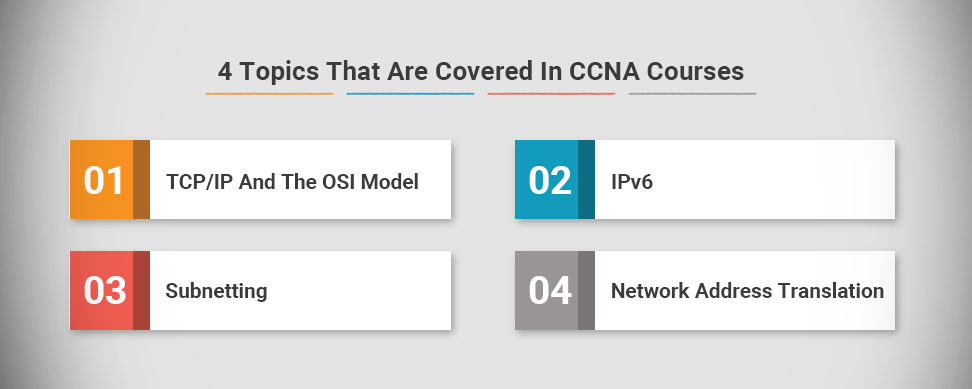
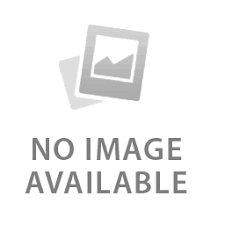
